Porosity in Welding: Identifying Common Issues and Implementing Finest Practices for Avoidance
Porosity in welding is a prevalent issue that often goes undetected till it triggers significant problems with the honesty of welds. This common defect can compromise the strength and resilience of welded structures, posing safety and security dangers and resulting in expensive rework. By recognizing the origin of porosity and carrying out reliable avoidance strategies, welders can substantially improve the top quality and reliability of their welds. In this conversation, we will certainly check out the vital variables contributing to porosity formation, examine its detrimental effects on weld efficiency, and go over the best methods that can be adopted to decrease porosity occurrence in welding procedures.
Common Root Causes Of Porosity

Another regular wrongdoer behind porosity is the presence of pollutants on the surface of the base metal, such as oil, oil, or corrosion. When these contaminants are not successfully removed before welding, they can evaporate and come to be entraped in the weld, creating flaws. Additionally, utilizing filthy or wet filler products can present contaminations right into the weld, adding to porosity problems. To reduce these usual reasons for porosity, detailed cleansing of base steels, appropriate shielding gas selection, and adherence to ideal welding parameters are essential methods in attaining high-quality, porosity-free welds.
Influence of Porosity on Weld High Quality

The presence of porosity in welding can significantly compromise the structural stability and mechanical residential or commercial properties of bonded joints. Porosity produces gaps within the weld metal, compromising its general strength and load-bearing capacity. These gaps serve as anxiety focus factors, making the weld extra at risk to fracturing and failure under applied tons. In addition, porosity can minimize the weld's resistance to deterioration and other environmental variables, additionally lessening its longevity and efficiency.
Welds with high porosity levels have a tendency to show reduced effect strength and decreased capability to warp plastically before fracturing. Porosity can impede the weld's ability to properly send forces, leading to early weld failing and possible security dangers in vital frameworks.
Finest Practices for Porosity Prevention
To enhance the structural honesty and quality of bonded joints, what details procedures can be carried out to decrease the occurrence of porosity throughout the welding procedure? Using the proper welding strategy for the specific product being welded, such as adjusting the welding angle and weapon setting, can even more avoid porosity. Routine assessment of welds and instant remediation of any type of issues determined during the welding procedure are vital techniques to avoid porosity and generate high-quality welds.
Significance of Proper Welding Techniques
Executing proper welding methods is vital in ensuring the architectural integrity and top quality of bonded joints, building upon the foundation of efficient porosity avoidance procedures. Too much warmth can lead to raised porosity due to the entrapment of gases in the weld swimming pool. In addition, using Full Article the proper welding criteria, such as voltage, present, and take a trip rate, is critical for accomplishing sound welds with minimal porosity.
In addition, the choice of welding procedure, whether it be MIG, TIG, or stick welding, need to align with the particular demands of the task to guarantee optimum outcomes. Correct cleaning and prep work of the base helpful site metal, as well as picking the right filler material, are likewise important components of skilled welding techniques. By adhering to these finest methods, welders can reduce the threat of porosity formation and produce high-quality, structurally sound welds.
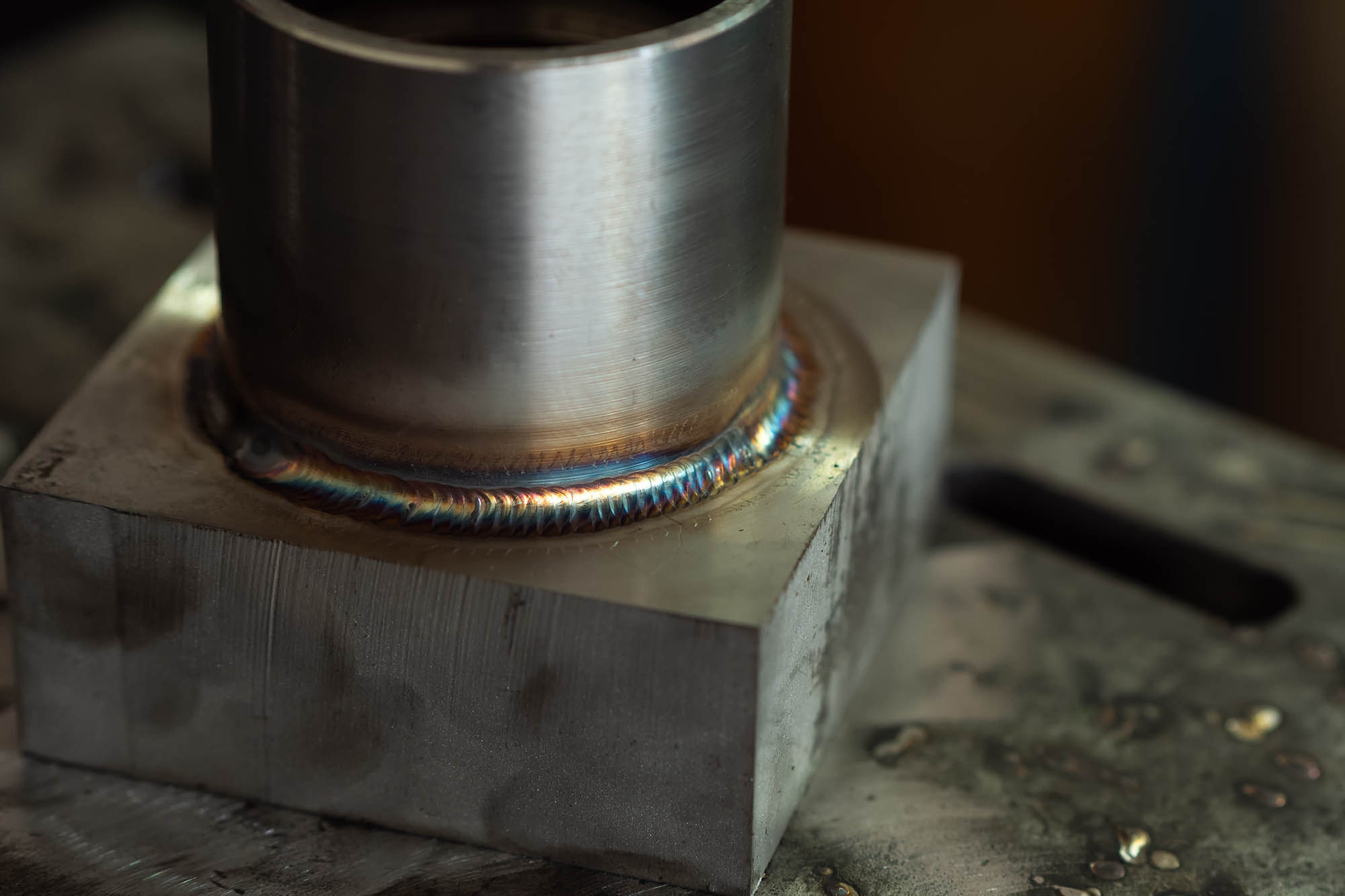
Checking and Quality Assurance Measures
Quality assurance actions play an important duty in confirming the integrity and reliability of welded joints. Examining procedures are necessary to find and protect against porosity in welding, ensuring the stamina and toughness of the end product. Non-destructive screening techniques such as ultrasonic screening, radiographic testing, and visual examination are frequently utilized to determine possible issues like porosity. These strategies permit for the analysis of weld top quality without compromising the see this integrity of the joint. What is Porosity.
Post-weld examinations, on the other hand, analyze the last weld for any type of problems, consisting of porosity, and validate that it satisfies defined requirements. Carrying out a thorough high quality control strategy that consists of thorough screening treatments and assessments is critical to decreasing porosity concerns and guaranteeing the total quality of welded joints.
Verdict
In final thought, porosity in welding can be a typical issue that affects the top quality of welds. By identifying the typical root causes of porosity and executing ideal practices for prevention, such as correct welding techniques and screening actions, welders can guarantee top quality and dependable welds. It is necessary to focus on prevention techniques to reduce the event of porosity and keep the stability of bonded structures.
Comments on “Discover What is Porosity in Welding and Its Result on Structural Stability”